The science of cartridge design
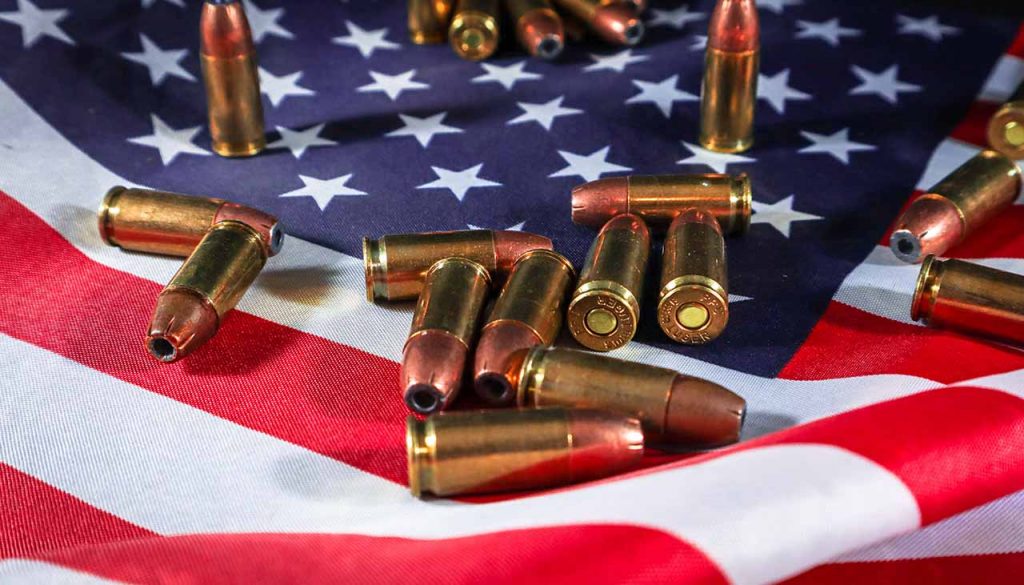
Cartridge design is a fascinating and complex science that combines physics, engineering, and materials knowledge to create an effective ammunition system. It all begins with the chemical composition of the propellant — and then it’s off to decide on bullet shape, size, weight, brass type, primer type and powder charge needed for optimal performance. The complexity doesn’t end there: cartridge designers must also consider how their design elements interact with firearms mechanisms like bolt motion cylinders or semi-automatic actions in order to maximize efficiency while reducing wear. In short — a great deal of precision goes into designing ammo cartridges! This blog post will explain more about this intricate process and delve deep into the realm of cartridge design science.
Overview of cartridge design components and their basic functions
When we talk about cartridge design, we are referring to a cylindrical (or sometimes rectangular) housing for either gas or liquid containers. The components of these cartridges make their essential items for camping, hunting, and many other outdoor activities. Here is an overview of the typical components involved in this type of design:
- Casing – This is the outer shell that holds all the internal components together. It is usually made from plastic or metal, with some designs featuring a combination of both materials.
- Valve – This component allows air or fluid to flow through the cartridge and out into its environment. Valves can be manual or automatic depending on the type of cartridge being used.
- Seals – These are rubberized seals that keep the internal components from spilling or leaking out.
- Springs – Springs are often used to control the flow of air or liquid through the cartridge’s valve, as well as for providing additional stability.
- Connector pieces – These connectors allow different sections of the design to join together and create a seal to prevent any leakage.
An examination of cartridge materials, such as plastic, rubber and springs
The material choices you make when selecting a cartridge can have a significant impact on its performance. Commonly used materials include plastics (such as polyethylene), metals (like stainless steel), and rubber compounds, though other advanced materials may be considered depending on your specific requirements. Let’s take a closer look at each type of material:
- Plastic – This is an incredibly versatile material that can be formed into almost any shape. It’s lightweight and provides excellent insulation, making it ideal for camping applications where weight and size are of paramount importance.
- Metal – Metals are strong and durable, but also heavy, which makes them unsuitable for most camping scenarios. They are however often used in cartridges designed to handle higher pressure or temperature conditions as they won’t degrade over time.
- Rubber – This is another lightweight material that is resistant to wear and tear, as well as provides good insulation from temperature changes. Rubbers come in a variety of compounds with different properties (such as oil resistance) to suit different needs.
- Springs – These provide the necessary pressure for a cartridge’s valves to open and close, as well as providing additional stability. Different types of springs are available depending on the application, with some featuring rust-resistant coatings for added durability.
Exploring the different types of cartridges available, including open-ended and closed-ended designs
There are two main categories of cartridges: open-ended and closed-ended. Open-ended designs allow fluid or gas to flow freely from both ends of the cartridge, while closed-ended designs restrict the flow in one direction only (typically with a valve at each end). Let’s take a closer look at how these two designs differ:
- Open-ended cartridges – These are typically smaller in size and are often used for camping, hunting and other outdoor activities. They offer convenience as their contents can be quickly replaced or adjusted without the need to remove the entire cartridge from its housing.
- Closed-ended cartridges – These are larger but provide greater precision when controlling air or fluid flow through a valve at either end. They’re also more suited to heavier-duty applications such as industrial processes where precise control is required.
How the shape of a cartridge can affect its performance in different situations
The shape of a cartridge can have an impact on how it performs in certain environments. For example, longer and narrower designs can have a higher resistance to clogging, whereas shorter and wider cartridges provide better flow characteristics. Similarly, the curvature of the cartridge can influence how it functions in certain situations; for example, curved sections are thought to reduce back pressure. Ultimately, the shape of your cartridge should be chosen based on your specific application requirements.
The importance of maintenance when using cartridges
Cartridges require regular cleaning and maintenance to ensure they continue functioning properly over time. It’s important to check all seals periodically for any signs of wear or damage, as well as remove any debris that may have built up inside the cartridge over time. If necessary, lubricate connectors and springs with appropriate fluids such as silicone grease or oil to ensure optimal performance. Finally, always store your cartridges in a cool and dry place to prolong their life.
Conclusion
Cartridge design is an essential part of many applications, from industrial processes to camping and hunting. Different types of materials provide different benefits depending on the situation, while the shape and size of a cartridge can influence its performance in certain scenarios. Additionally, regular maintenance is needed to keep cartridges functioning properly over time. By understanding these concepts, you’ll be able to make informed decisions when selecting the right type of cartridge for your application.